Recently we blogged about how appearance affects color. In this article we look at some of the characteristics that impact an object’s appearance, such as texture, gloss, transparency, and special effects, and explain why it’s crucial to describe appearance in the early stages of the design workflow.
While 3D programs have attempted to address appearance aspects for years, there has been a missing link in virtual product design: the ability to integrate characteristically “true” real-world materials. To address this issue, we introduced the Appearance Exchange Format in 2016, an incredibly accurate way to store and share color AND appearance data.
AxF is a vendor-neutral file format that can be used in virtual design programs to ensure a consistent look and feel. It goes beyond color to help designers create full-scale digital mock-ups to virtualize complex materials like special-effect paints, leather, plastics, fabrics, wood, and metals, just to name a few. Using AxF, brand owners, designers, and manufacturers can digitally represent color and appearance data at all steps in the design-to-production workflow, reducing design time and approval cycles.
Lumiscaphe is one of many 3D software companies to use AxF in their rendering software. We had the opportunity to sit down with Lumiscaphe’s co-founder and product manager to learn more about photorealism, and how their latest version of Patchwork 3D relies on AxF to transform CAD data into photorealistic 3D models for industrial use.
Q: What is photorealism, and how is it revolutionizing the way companies design, prototype, and market products?
A: Photorealism refers to a 3D virtual rendering that looks like a true photograph, so you can see exactly how the product will look during the design phase. Physical prototypes are expensive and time consuming to build. Photo-realistic rendering allows you to detect design issues and make design choices without (or with fewer) physical prototypes.
Photorealism also makes it possible for customers to preview customization choices. A car, for example, can have millions of possible combinations due to many options multiplied by customization possibilities. You cannot make millions of cars and take millions of pictures of the car! With photorealism, car manufacturers can show customers exactly how their configurations will look – the whole car, not just close ups on the specific options.
Q: Which industries have the greatest need for physically realistic details in their renderings?
A: Any industry where there is a need to see or to show what the product would look like, without having to make the actual, physical product first. The more physically correct you are during the design phase, the sooner you can detect issues and fix them, saving a lot of time and money during product development. And, the more physically realistic you are during the sales and marketing stage, the more satisfied your customers will be when they receive a product that looks as expected.
Q: What types of materials are the hardest to develop renderings for?
A: Composite materials, which are made of a mix of different materials, are the hardest because each material can behave differently depending on the light source, observation point, and patterns. For example, a car paint that is made of different layers and special effect pigments that all behave differently with light changes can pose a challenge.
Q: Why did you decide to integrate AxF in the latest version of Patchwork 3D?
A: There are two main reasons. First is interoperability. AxF is the standard for material definition for rendering. Our customers want standards. If a material OEM provides them with an appearance definition file of materials, it will be using a standard.
Second is automation and industrialization. CGI artists can easily create appearance characteristics using our software, using different techniques. Engineers don't. They need a process. For example, they will use a TAC7 to scan samples of materials and will put the result, an AxF file, directly into our software, ensuring a consistency in the process and making it objective and not subjective. The product visuals will be more physically correct.
Q: What value does AxF bring to your customers?
A: Our solutions are meant for industries. We try hard to ensure that everything in our software is defined using physical values and measurements. Everything is metric, scale 1:1, calibrated. If anything can be automated, objectively defined, we do it. AxF has been designed with the same philosophy. The use of AxF reinforces this perception of an industrial-centric company.
Q: Which big trends in virtual design are you following?
A: Lumiscaphe believes virtual reality will bring with it new uses and tools to make designers’ work easier. Those who are facing expensive and time consuming physical mock-ups can use it to save time and to improve collaboration between design and development teams, whether at the same site or remote.
Since more models can be reviewed in the same period of time, we also believe virtual reality will increase diversity of first design cycles. By lowering the cost and duration of each cycle, design reviews will be improved as several design cycles can be done at the same time.
Right now, virtual reality is a must-have for automotive markets, and other industries clearly understand the economic stakes.
Are YOU Ready to Harness the Design Power of Virtual Design?
To learn more about how AxF and the TAC Ecosystem can help create a more optimized and trusted workflow for your designs, visit our website. To see how AxF helps Lumiscaphe render photorealistic 3D models in Patchwork 3D, download a free trial here.
Featured Color Management Solutions
Learn more about the products featured in this blog:
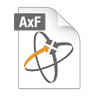