COVID-19 has stopped many industries in their tracks, textiles included. Travel bans and shelter-in-place orders are forcing vast, inter-connected supply chains to rethink the way they work.
For brands that were already looking for new ways to achieve accurate color and speed time to market, this could be an opportunity. This global pandemic may help the apparel industry make important decisions to change the way it works – for the better – not only to get through this crisis, but to also create more efficient, cost-effective, and sustainable ways to manufacture clothing.
Maybe it’s time to take a real look at digital color.
Can Digital Color be Trusted?
3D design is an exciting technology for brands hoping to reduce waste for a greener footprint and accelerate design to keep up with customer trends. Many designers have already embraced Adobe digital color tools and CAD 3D programs.
However, moving to a digital textile and apparel workflow also raises a few concerns:
-
What is the best tool to capture accurate color and appearance for use in digital designs and 3D virtualization programs?
-
Can on-screen color be trusted to make critical color decisions and approvals?
The answers are interwoven. Yes, digital color can be trusted, but textile brands need to employ proper measurement and calibration tools to ensure color fidelity throughout design and production.
Tools to Bring Color into a Textile Workflow
In the textile industry, using a spectrophotometer for textiles to capture both color and appearance on a physical sample has greatly improved quality, consistency, and speed to market. To make color approvals on-screen, the digital color file must also be color-accurate when it is imported into the design software.
This requires the right textile color measurement device. While a sphere spectrophotometer is ideal for textile colorant formulation, a 45⁰:0⁰ is better suited to capture digital color for on-screen color approvals.
For Formulation: Use a Sphere Spectrophotometer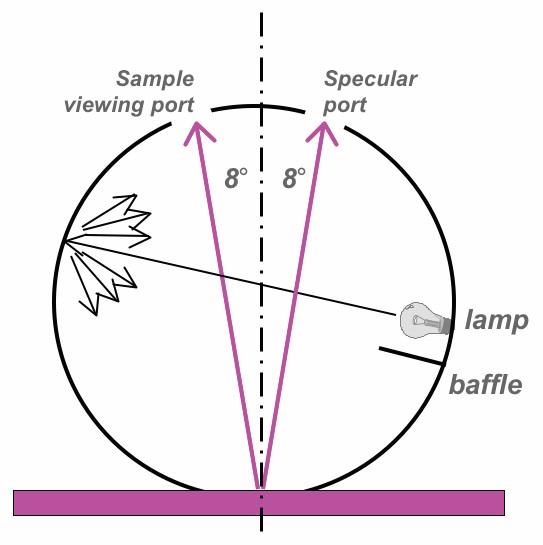
Typically, brands use a sphere (d:8⁰) device to measure textile swatches and capture spectral data for use during dye formulation. Spherical in shape, these instruments are lined with a highly reflective, very low gloss, white matte surface.
As the device illuminates the object diffusely from all directions, more than 99% of the light is reflected and scattered randomly in all directions. The detector receives the reflected light at an 8° angle from the object’s surface, diminishing the effects of non-color related material variations like texture and weave.
While ideal for creating and controlling color at the lab dipping and dye formulation stage, a sphere device creates a rather artificial viewing situation because it over-illuminates the sample to disregard the visual effect of texture. Capturing color with a sphere creates an appearance scenario similar to evaluating color during a snowstorm: diffusely illuminated with evenly distributed light coming from all directions.
Bottom Line: A sphere is the right device to capture spectral data from physical textiles samples, but the digitally-colorized images it captures are too light and de-saturated for use for on-screen color decisions.
To choose the best tool for on-screen color in a textile workflow, we look to the print and packaging industry.
![]() |
This image illustrates how capturing color with a sphere creates a diffusely illuminated scenario with evenly illuminated light coming from all directions. |
For On-Screen Color Decisions: Use a 45⁰:0⁰ Spectrophotometer
To avoid looking directly into the specular highlight (45⁰:45⁰), we humans typically tilt the sample or shift our observation position to achieve a 45⁰:0⁰ or 0⁰:45⁰ geometry. This is the basis behind 45⁰:0⁰ geometry instruments, which have been used for years to calibrate and control the graphic design workflow to ensure the best color match from camera to display and display to print.
A 45⁰:0⁰ device represents a viewing condition that mimics how humans evaluate color in everyday situations – illuminated from 45⁰, and viewed at a 0⁰ angle. In essence, a 45⁰:0⁰ device “looks” at the color just as a colorist would visually evaluate color in a light booth. Enabling photorealistic 3D garments reduces the need to produce samples and prototypes for visual evaluation.
Bottom Line: Measurements illuminated and captured from a single angle provide realistic color data for optimal on-screen color reproduction. When used for digital color in a textile workflow, a 45⁰:0⁰ can enable remote approval for product color without creating and shipping physical lab dips.
The image to the right emulates how a 0⁰:45⁰ (left) and a sphere spectrophotometer (right) capture color data from the same fabric sample. The diffuse illumination of the sphere succeeds in minimizing the apparent directionality of the weave in the sample, resulting in a measurement of pure color; absent the effects of the texture.
The Best of Both Worlds: MetaVue VS3200
The MetaVue VS3200 is an imaging spectrophotometer that captures spectral information for every pixel in the measured image to bring textile color data into a digital workflow. Beyond having the proper 45⁰:0⁰ illumination design, the MetaVue VS3200 can capture color data like typical human vision. Rather than over-illuminating and averaging all the various shades like a sphere, the MetaVue VS3200 disregards small shadows, highlights, and off-shade spots in the surface of the physical target, thereby capturing true color as the eye sees it.
![]() |
Retail paint matchers also use a 45⁰:0⁰ instrument because it generates color matches that will meet the appearance expectations of customers forsamples with multi-colored patterns and texture. |
Designers can use the MetaVue VS3200 to capture digitized color data for their digital designs to accurately represent color, texture, and appearance in design and CAD 3D programs. The resulting 3D designs allow brand colorists to make product decisions and approve color digitally without the associated time and shipping waste of handling physical lab dips and creating prototypes.
Tools to Ensure Accurate On-Screen Color
As designers, suppliers, and brands begin to make color decisions on-screen through Adobe tools and CAD 3D programs, the need to display color accurately on screen becomes even more important. Since laptop screens and computer monitors are the windows into this digital world of color, accurate and consistent Color Management tools must also be used to ensure optimal color representation on screen.
![]() |
Our Monitor Calibration blog explains how easy it is to calibrate your monitor using the X-Rite i1Display Pro and i1Profiler software to view optimal color of digital designs. |
Need Help Starting Your Digital Color Textile Workflow?
We know every workflow and supply chain is different. Get in touch for expert guidance on how to choose – and use – the right color measurement and calibration tools to ensure color fidelity, on-screen and throughout production.
If you’d like to see how our Total Appearance Capture (TAC) Ecosystem is helping 3D designers bridge the gap between physical and digital, read our How Universities are Driving the Future of Apparel Design blog.