Black Friday. Not only is it the much anticipated start to holiday shopping, it’s also a day manufacturers have been preparing for all year long.
Whether mass-producing holiday cards, candy canes, plastic toys, or festive clothing, accurate color is a must. Manufacturers can’t ship two of the same toy if they won’t match on the showroom floor, and holiday sweaters that are a shade off will end up at a discount store instead of a fashion boutique.
Perfection is especially important for brand colors. Who will be left with the cost of wasted time and materials if color doesn’t pass brand owner expectations?
A tolerance is the acceptable amount of color variation between the color that is specified and the color that is manufactured. While color tolerances can vary between industries, they are important in every manufacturing process. You can learn more in our Tips to Define Tolerances blog.
Today we’ll look at how managing color to meet tolerances is important for the paper, plastics, textile, and glass industries as they prepare for Black Friday’s shopping mania.
Wrapping Paper and Holiday Cards
Holiday cards and wrapping paper are a big part of the season. Sometimes packages are even prettier than what is inside! But achieving those perfect holiday colors – and keeping them consistent during large paper and card print runs – is not an easy task.
Printing accurate color requires a tight color managed workflow that can match the appearance from input (designer’s file) to output (printing press). Since each device uses slightly different CMYK or RGB formulas to create the same color, printers rely on ICC profiles to help with this conversion between devices.
Printing presses can run anywhere from 4 to 7 process color inks, and mixing them to create the perfect holiday colors isn’t always easy… or possible. In these cases, printers rely on spot colors, which are premixed inks, each requiring its own plate on press. Brand colors like Coke Red usually require spot inks to achieve color perfection.
A consistent and repeatable color managed workflow makes it much easier for manufacturers to produce mass quantities of colorful holiday cards and wrapping paper in time for the Black Friday rush. Many manufacturers are adopting an Extended Color Gamut approach (also called Fixed Color Palette Printing) that uses CMYK plus Orange, Violet and Green or Blue to achieve the vast majority of special colors with process printing.
Plastic Toys
Color is becoming increasingly important in plastics, and tolerances continue to tighten. From Star Wars™ action figures to Lego® bricks, the color has to be right or the toys won’t make it to the store shelves. Many brands are incorporating special effect colors into their products, further complicating the manufacturing process. Color measurement systems can help plastics manufacturers ensure that their colors remain in tolerance.
Did you know most plastic toys start as synthetic pellets? When manufacturers get a shipment of pellets to create a plastic toy, they use a color measurement device called a spectrophotometer to ensure that the pellets they receive are the correct color. Then they melt and mold them into the final product. This heating process can change the color, so spectrophotometers are used at many points during production to ensure that color remains within tolerance from incoming materials to retail shelves.
Holiday Candy Wrappers
Transparent films also start with plastic pellets. When extruding these pellets to produce transparent films for product packaging and cellophane wrappers, manufacturers must monitor visual light transmission and haze to see how they are affecting the color. This requires a special spectrophotometer that can measure in transmission mode.
Festive Clothing
Although holiday sweaters are all the rage these days, their color needs to be in tolerance to make it to store shelves. Did you know that each piece of the garment, from sleeves to buttons to trim, can be manufactured in different plants around the globe and sewn together someplace else entirely? Unfortunately, those fabrics and accessories often don’t match. During assembly, clothing must be evaluated to ensure that the sleeves match the collar, and the trim matches the buttons, under any possible light source.
Metamerism is an optical phenomenon in which items appear to match under one light source, but not under another. Have you ever left the house wearing what you think are two black socks, only to realize once you hit daylight that one is dark brown? The same happens when assembling clothing. Before shipping, manufacturers must use a light booth like the Judge QC to ensure their garments match in every possible lighting condition, including the store, home, and even outdoors.
Store Windows
Window shopping is a tradition for many families. Whether you’re walking through New York City or a small town in Oklahoma, the holidays come to life through store windows. Did you know that the color of the glass that separates you from the beautiful decorations must also be carefully controlled? As you can imagine, measuring glass can be a challenge.
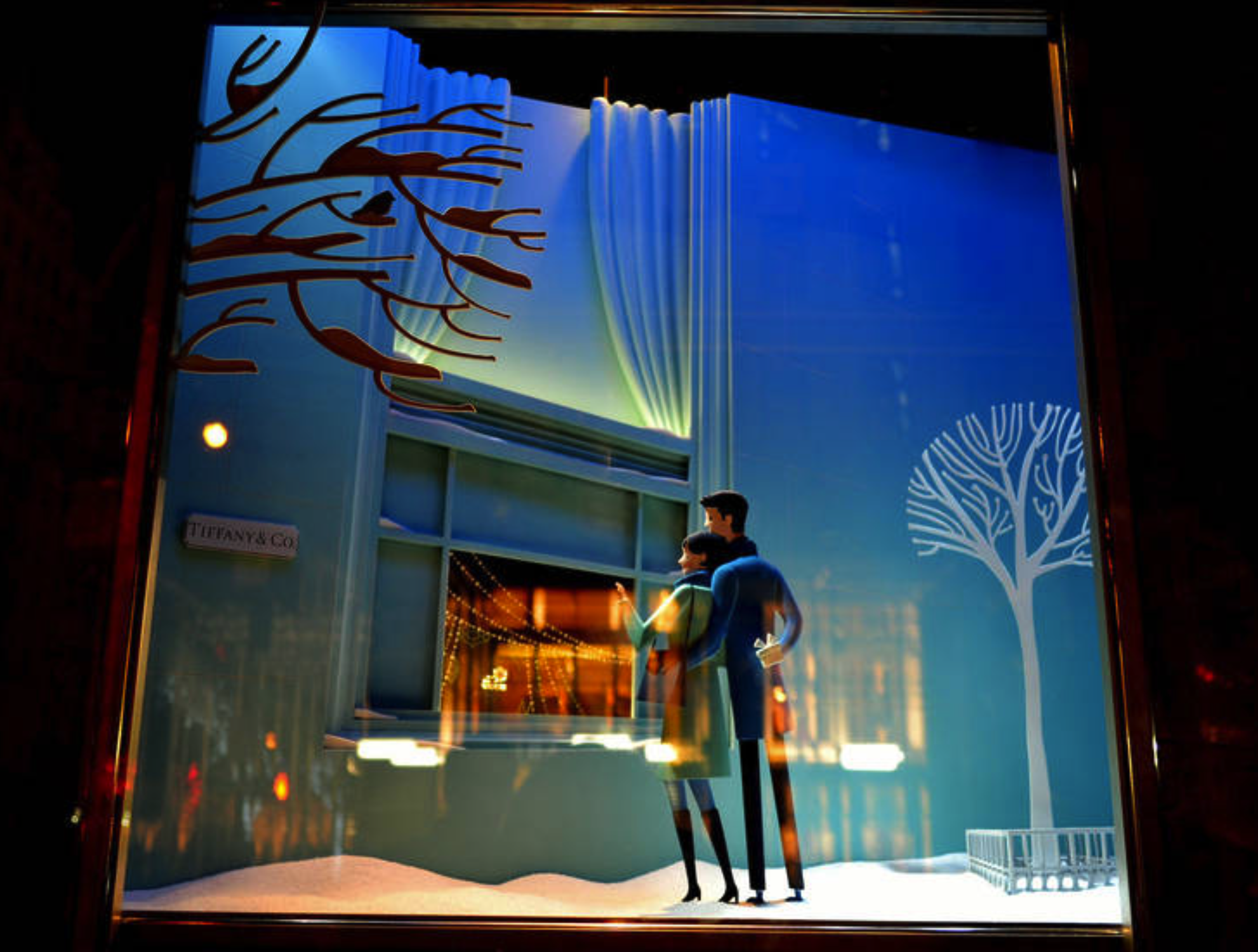
This photo of a 2015 Tiffany & Co. holiday window shows the reflective properties of glass that make color so difficult to control during production. Photo courtesy of timeout.com.
X-Rite’s inline glass color measurement system uses a non-contact spectrophotometer to measure the production of glass and other materials directly on the production machine. The device is mounted on a frame above the glass and illuminates the pane at a certain angle, measuring the reflected light at the other side. The measurement is displayed as a spectral curve so operators can monitor the process and make adjustments or stop production it anything moves out of tolerance.
Will You be Thinking About Product Color on Black Friday?
While you may not consciously realize it, color plays a big role in the products you will choose. Even if you overlook the technical aspect of maintaining those perfect holiday colors, to manufacturers accurate color is one of the most crucial components of staying in business. X-Rite is here to provide the tools, resources, and training to make producing holiday items easier than braving the crowds that rush out to buy them.