Color measurement devices have been around since the 1940s, but they’ve come a long way since then.
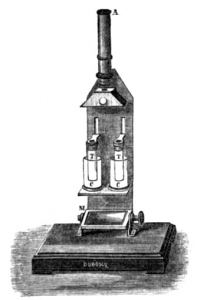
Built by Jules Duboscq in France in 1870, the Duboscq colorimeter was one of the first color measurement devices.
The earliest instruments were colorimeters, which used red, green and blue filters to simulate the tristimulus response of the human eye. Back in the ‘40s, they were pretty expensive so few people had access to them. Even more expensive were spectrophotometers, which measure color by sampling light at very narrow intervals across the visible spectrum.
Modern technology has paved the path for specialty devices for every kind of industry, and lower prices make color measurement devices accessible to everyone, from hobby photographers to car manufacturers.
Today we’ll look at the difference between colorimetry and spectrophotometry and the geometries that define each.
Colorimetry vs. Spectrophotometry
Color measurement instruments are either colorimeters or spectrophotometers.
A colorimeter is a three-channeled device that “sees” color exactly like the human eye. In essence, it quantifies the tristimulus red, green, and blue components of each measurement and uses that data to determine a color’s location in color space using either L*a*b* or L*C*h° metrics. For some industries, this is sufficient data. For others, it may fail to identify crucial color matching errors.
Spectrophotometry, or reading a sample’s response across the visible spectrum, is the best way to obtain data for color formulation and to ensure quality. Spectros work by filtering light into very narrow bands of color, which pass back up through the instrument’s optics and into a receiver where they are analyzed.
Each band, from 400 to 700 nanometers, is analyzed and recorded as a reflectance curve… the color’s “fingerprint.” Here is the reflectance curve of a red ball. It appears red because it is reflecting mostly the red wavelengths of light. Only a small percent of incident light from the blue and green portions of the spectrum remains. As it moves from the yellows into the true reds, the curve approaches 80%.

No two reflectance curves are exactly the same… unless they are two readings of the same pigments or dyes.
Color Measurement Device Geometries
If everything were flat, matte, and smooth, a basic instrument is all we would need. But there are so many surfaces to measure – opaque, reflective, transparent, curved, textured and variegated – that one device can’t do it all.
Single Angle 0°:45° Color Measurement Devices
The most popular geometry for quality control and product assurance in many industries is the 0°/45° (pronounced zero forty-five), or 45°/0°. Lamps are located at a 45° angle with respect to the sample and the receiver, or reversed with the receiver at 45° and the lamp overhead. Either way, there is a right angle, bisected at 45 degrees. This device most closely replicates how humans see color because it excludes gloss from the measurement.
0°/45° instruments perform well with most surfaces, dyes, and pigments.
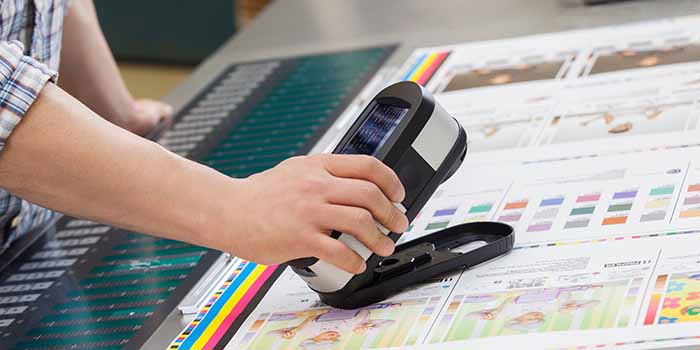
The X-Rite’s eXact Family is ideal for measuring print samples to ensure color accuracy and consistency.
Spherical Color Measurement Devices
Another common geometry is the sphere, also known as a diffuse 8°, or just D8. It’s a little more complicated because it can include gloss as part of the measurement.
Inside the instrument is a lamp that shines at the far, curved wall instead of directly at the sample. The light is scattered by the wall thousands of times, illuminating the sample from every direction, taking into account every variation in texture and gloss. A small trap door called a specular port can be opened and closed to allow gloss to escape.
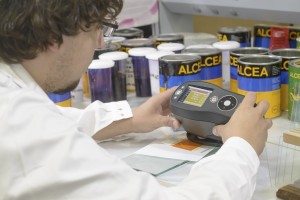
A sphere spectrophotometer such as X-Rite’s Ci64 series is ideal for formulating ink, pigment, and dye recipes, independent of gloss and texture.
Multi-Angle Color Measurement Devices
Many industries, including cosmetics and automotives, are very interested in special effects like pearlescents and metallics. These pigments make the paint look different at different angles. We’ve all seen cars that appear to change colors depending on where you’re standing or the angle of the sheet metal.
Gonio-spectrophotometers were the first multi-angle devices that could see color shifts the way we do, but they were very big, and very expensive. Today we have portable, handheld, multi-angle instruments that can measure a surface from many angles. They work with a single point of illumination, typically at 45 degrees, and a number of different receivers that capture and record the light as it scatters in different directions.
In addition to the auto industry, these instruments are used in cosmetics for fingernail polish and eye makeup, and other industries that produce materials with interesting optical properties.
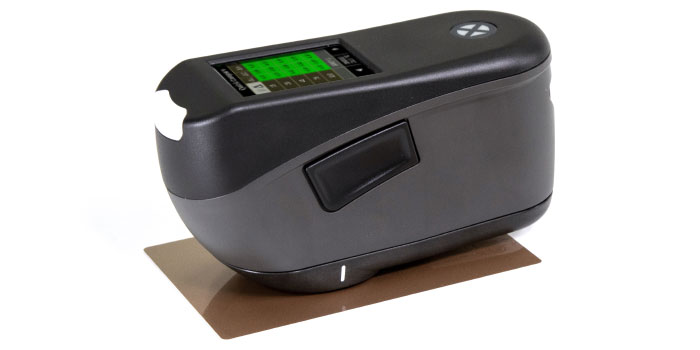
The MA-5 QC multi-angle device from X-Rite is exceptional for measuring metallic, pearlescent, and other complex special effect finishes.
So… Which Color Measurement Device to Choose?
Modern color measurement devices come in a variety of shapes and sizes, and they’re used in a lot of different industries, including food, medical, dental, photography, paint, plastics and even pharmaceuticals. They can be manual or self-scanning. Some take only one measurement at a time and display it on a computer screen, while others have built in computers. Some are even non-contact, which means they can measure parts from a distance as they move down the production line.
With at least a hundred different types of instruments to choose from, how do you pick the one that’s best for you?
- Start by considering the type of materials you’ll be measuring. Are your samples smooth or textured? Large or small? Are they flat or curved? Made with special pigments, like metallics or pearlescents?
- What type of environment will you measure in? Can the samples be handled without damage?
- Are you part of a global color measurement group that requires exceptional quality and tight consistency? Or can you get by with a little less precision because you’re a standalone operation?
- Does the data need to be stored? How about shared worldwide?
- What kind of speed and automation do you need?
- And, of course, repeatability is critical, as probably is price.
Most importantly, you need to consider your industry to decide which color measurement device is right for you.
For print and packaging, check out our recent blog.
Featured Color Management Solutions
Learn more about these featured products:
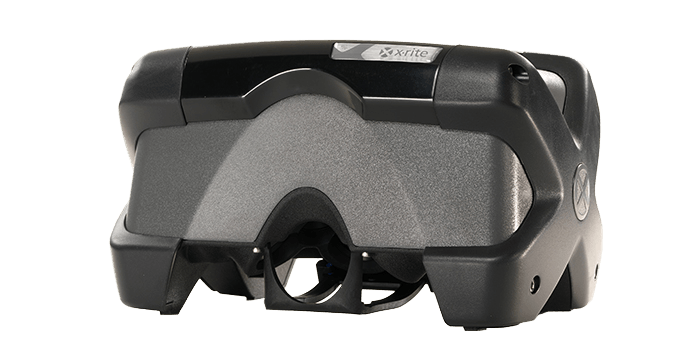
VS450
The VS450 is a unique, non-contact color measurement instrument for measuring color accuracy of a variety of wet and dry samples including cosmetics, paints, plastics, powders and food.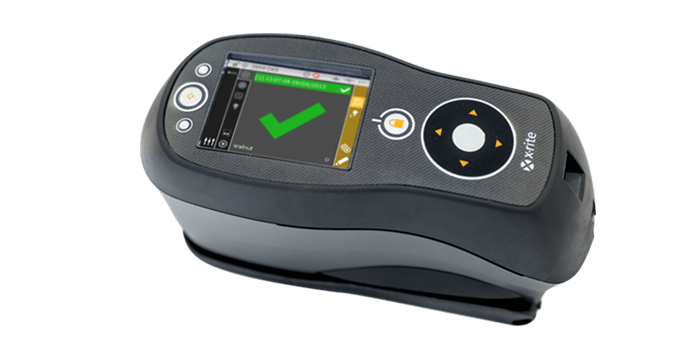
Ci64
The Ci64, X-Rite’s most precise handheld sphere spectrophotometer, is available in three models: with simultaneous SPIN/SPEX, correlated gloss, and a UV option.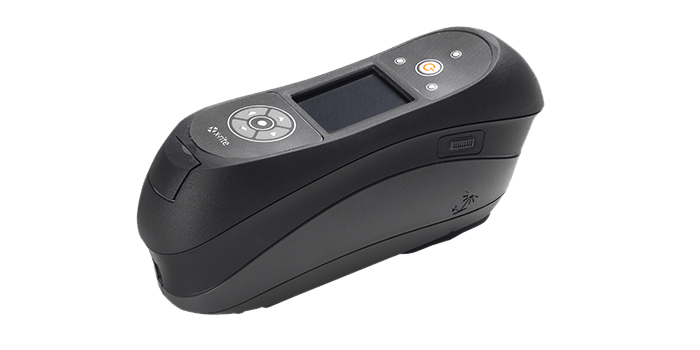