Did you read our blog: Are You Using The Right Tolerancing Method? If not, check it out. Today we’re taking the topic one step further to investigate how tolerances are chosen in different industries.
A pass-fail tolerance is the amount of color variation that is considered commercially acceptable. In part, tolerances are driven by customer expectations. While color tolerances are very tight in the automotive, plastics, and paint & coatings worlds, they can be much less strict in other industries.
For example, if you’re producing a vehicle, everything from the bumper to the door handles to the steering wheel and dashboard must match unconditionally, regardless of lighting conditions. That’s why the pass/fail limits for automobiles are very, very stringent… often 0.5 or less in a CMC calculation. Some automotive industries even use their own proprietary methods to achieve these tight tolerances.
But tolerances must also reflect the capability of the production processes. A delta E CMC setting this small makes it much harder to achieve expectations for accurate and consistent color. In the auto industry, the processes for painted or injection-molded parts are highly capable. They can make very small iterations of the same part over and over again with the same precise color control.
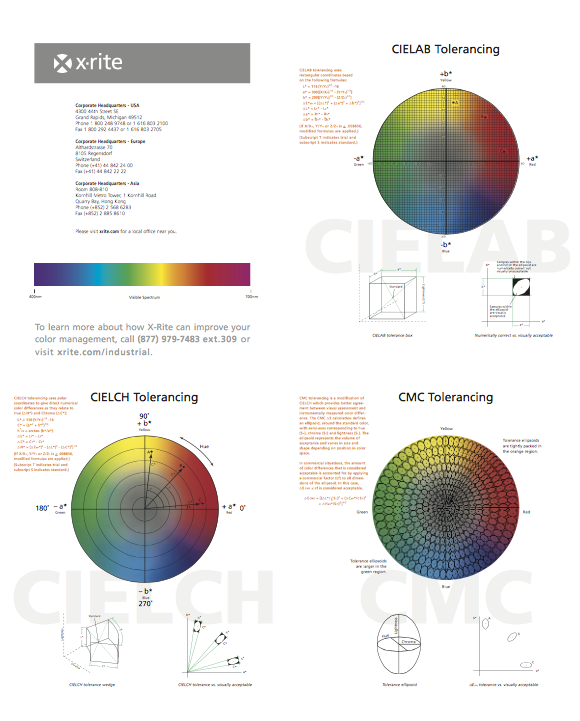
Check out this chart for help understanding the differences between CIELAB, CIELCH, and CMC tolerancing.
Unfortunately, it’s not that easy in other industries.
Take printing, for example, where the standards may be G7, SWOP, or GRACol. Other master numbers might come from an OK sheet or an approved press pull. But since a printing press isn’t capable of achieving a tolerance anywhere near that of a paint process on a consistent basis, most printing applications don’t even attempt a commercial factor of 0.5. They’d be throwing away virtually everything they made!
Printing industry standards are usually L*a*b or LCh, Delta E CMC, or often simply delta E. But the typical observer setting is D50 lighting, 2-degrees, as opposed to D65/10 for auto. The typical printing pass/fail standard is a delta E CMC of 2.0 or more. In some processes, it may be as large as 5.0. Print tolerances must be this relaxed because the process simply can’t do better on a consistent basis.
As you look at other industries, such as textiles, furniture, wall coverings, or retail paint, you’ll find that those who do color well establish good standards. They know that setting the delta E CMC too low means they won’t be able to produce sellable products at a good cost.
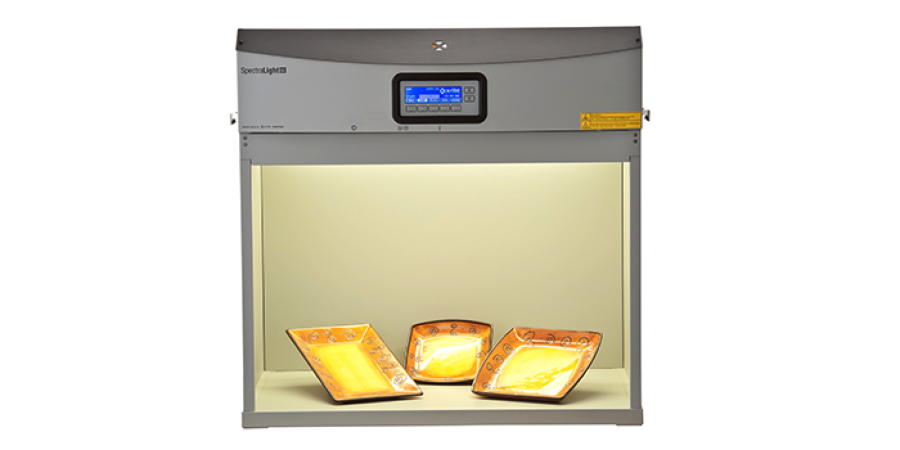
Visually evaluating the color of painted ceramic plates in the SpectraLight QC light booth.
In the end, it’s a balance between process capability and customer expectations… a buy-sell agreement between how accurately the customer wants you to make it, and how much they’re willing to pay.
To set achievable tolerances, you need to do your homework.
- Find out what lighting is considered important in your industry.
- Evaluate your processes and how capable they are.
- Look for established standards that you should follow, such as ISO, ASTM, SNAP, GRACol, G7, A2LA and/or AATCC.
- Find out what your competitors are doing.
- And talk to your customers. After all, isn’t your primary goal to make them happy?
To learn more about tolerancing or for advice on how to achieve yours, get in touch or consider our Fundamentals of Color And Appearance training seminar.
You may also be interested in reading our very popular blog Tolerancing In Flexo And Offset Printing.
Featured Color Management Solutions
Learn more about these featured products:
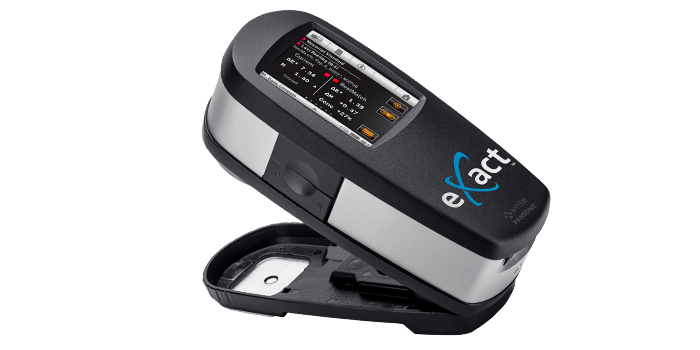
eXact
The new eXact combines industry-leading functionality with an easy-to-use interface to deliver the best solution yet for controlling, managing, and communicating color across the entire color workflow.
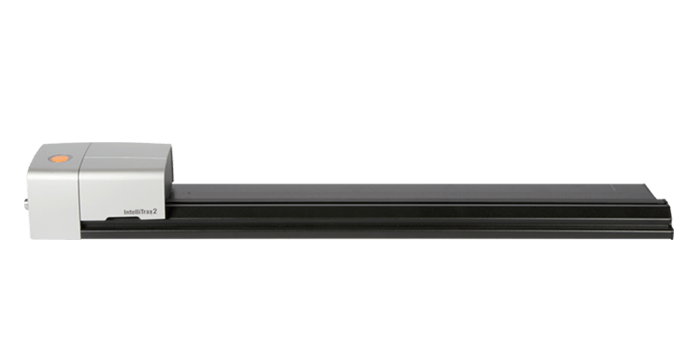
IntelliTrax2
Scan the color bar on a typical press sheet in less than 10 seconds. IntelliTrax2 is the ideal color management solution for high-end, high-speed printing/converting operations.
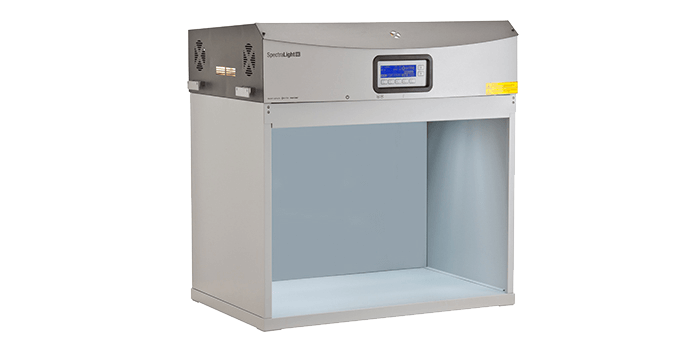